Tracking PMs: With And Without Fullbay
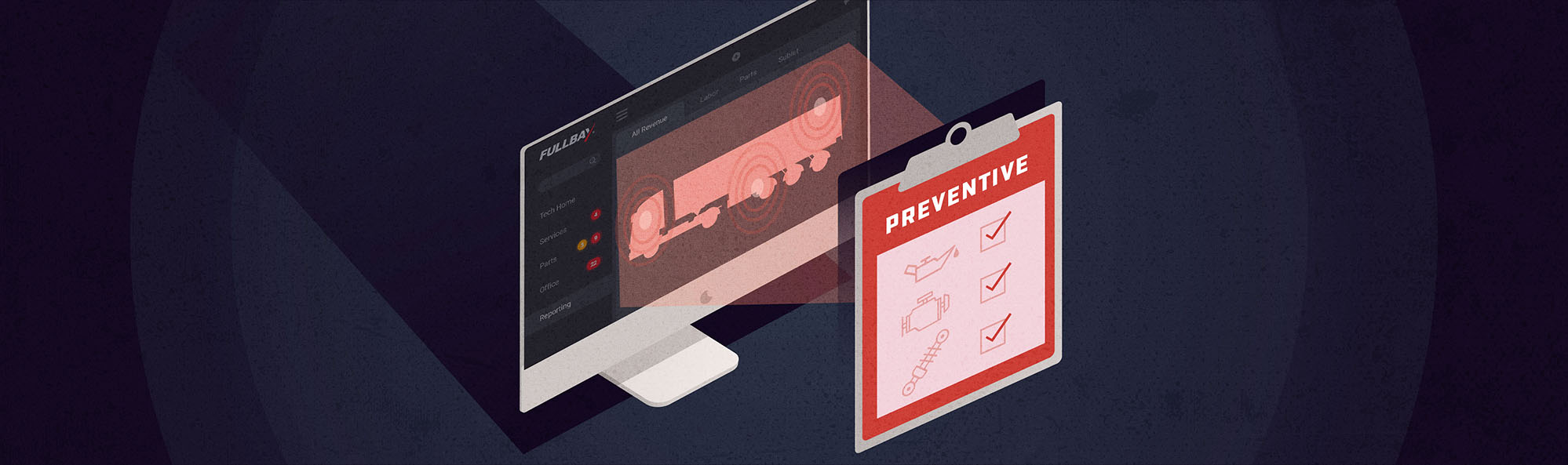
You track preventive maintenance, right?
If you don’t, stop reading this article immediately and read this one instead.
Tracking preventive maintenance (or PMs) is one of the single most important things you can do for your customers, and therefore one of the most important streams of revenue you can secure for your shop.
What’s so great about preventive maintenance? The key word here is preventive. Vehicles and equipment are similar to humans in one regard: they’re easier to treat before they get sick or break down. Bringing a truck in for preventive maintenance is very similar to going to the doctor for a yearly checkup. You can spot things before they balloon into problems.
Shops love PMs because they’re generally a steady stream of work. Fleet managers love PMs because they maximize uptime, minimize downtime, and keep vehicles of all stripes running at their optimal capacity.
But if you’re going to perform PM work, you need to track it. You need to know when each vehicle in a fleet is due for this and that.
Now, there’s two ways you can go about this. One involves spreadsheets, paperwork, and guesstimating, and it’s horrifying beyond words.
The other involves Fullbay.
Let’s dig in!
TRACKING PMS THE OLD-FASHIONED WAY
For the purpose of this article, we’re defining preventive maintenance as scheduled maintenance that is delivered at an interval. Intervals could apply to a measure of time, like months; it can also apply to miles traveled or engine hours.
So, to effectively track PMs, you need to document and update the mileage, engine hours, and amount of time that has passed since a vehicle’s last visit. You’ll use these to determine (usually based on manufacturer recommendation) when a vehicle is due for things like:
- Oil changes
- Fluid levels
- Tire changes
- Electrical system checks
- And so on!
You know that a particular type of engine and chassis—let’s say it’s a type of bus—require an oil change every 5,000 miles. You want to recommend PM work to a customer with a fleet of 30 buses.
These buses all have different routes; they rack up the mileage at varying rates. So it’s up to you to figure out when each of those 30 buses is probably going to hit 5,000 miles—or bugging your customers over and over to find out what mileage they have on their vehicles.
If you’re doing this on your own, this usually means spreadsheets. It probably doesn’t sound so bad for one or two trucks, but if you’ve got a sizable amount of business…well, picture yourself doing this for 100 vehicles, or 150. Then picture yourself calling the fleet managers to make arrangements each time you guestimate a vehicle needs some work.
You’d never get away from the office, and worse, asking your customers for this information over and over again gives them more work to do. Why make their lives harder when they already have enough to do?
TRACKING PMS WITH FULLBAY
All right, that was pretty scary. Let’s look into a far more effective way to track PMs, one that doesn’t end with you glued to the computer or phone.
Much like service orders, Fullbay lets you build out types of PMs. Every single unit type has a different combination of components and systems. Think engines, chasses, batteries, and so on. You can build a PM around those components and apply that PM to every single vehicle that contains them. This makes it easy to apply a specific type of PM service to a specific type of vehicle.
If, for example, you see that oil changes are your #1 revenue driver, you might decide that you should add oil changes to your PM services. You’ll create a new service type, detailing what type of oil you’ll use and how long it will take (say one hour), and what kind of interval you want between oil changes (number of miles or engine hours or timeframe). You can apply that service type to everyone with a specific type of engine and chassis (say, buses). That’s it; you’ve created a type of PM. and it will instantly apply that service type to every single bus with that engine and chassis.
If you’re using Fullbay GPS, the app will alert you if a particular unit is approaching the threshold you set. Depending on how you configure it, the PM will either move into the Upcoming Repairs tab or the app will ask you if you want to add the necessary work to a service order you’re creating.
If you’re not using Fullbay GPS, you have two ways to enter a vehicle’s mileage. Fleets can update their mileage in the Customer Portal; if they don’t, your techs will mark down a vehicle’s mileage and engine hours when it reaches the shop. Because everything is in Fullbay, you’ll be able to see when units are coming up on their necessary maintenance.
In other words, Fullbay and GPS data make for a much richer and seamless customer and shop experience.
HOW TO RUN A PM IN FULLBAY
So, now that you’ve got your PMs set up, how do you actually run one for the bus that just arrived in your shop?
It just takes three steps.
- Click the “Pending Repairs” tab and review PM work that is Pending, Late, or Scheduled
- Click the PM you want to schedule or perform
- Click “Create Service Order”
Since the type of PM you’re performing has already been configured with a specific rate, parts, labor, and so on, you’re good to go. The PM instantly converts to a service order that is ready for authorization or to start work.
And that’s it. The work of hours is condensed into three simple steps.
What could you do with the time you save on that task?
Seriously, though, what could you do? Catch your kid’s soccer game? Grab a cold one with some friends? Or maybe just relax on the couch for a minute, because all of us need to chill out sometimes.
TRY IT THE FULLBAY WAY
It’s true: Fullbay loves preventive maintenance. But that’s not everything we do—we’re also big fans of increasing tech efficiency and helping you run a more productive and profitable shop in general.
If you like what you’ve seen from our PMs, give our free demo a try! We’d love to show you what we can do.