Putting the Heavy and the Metal Into Heavy Metal
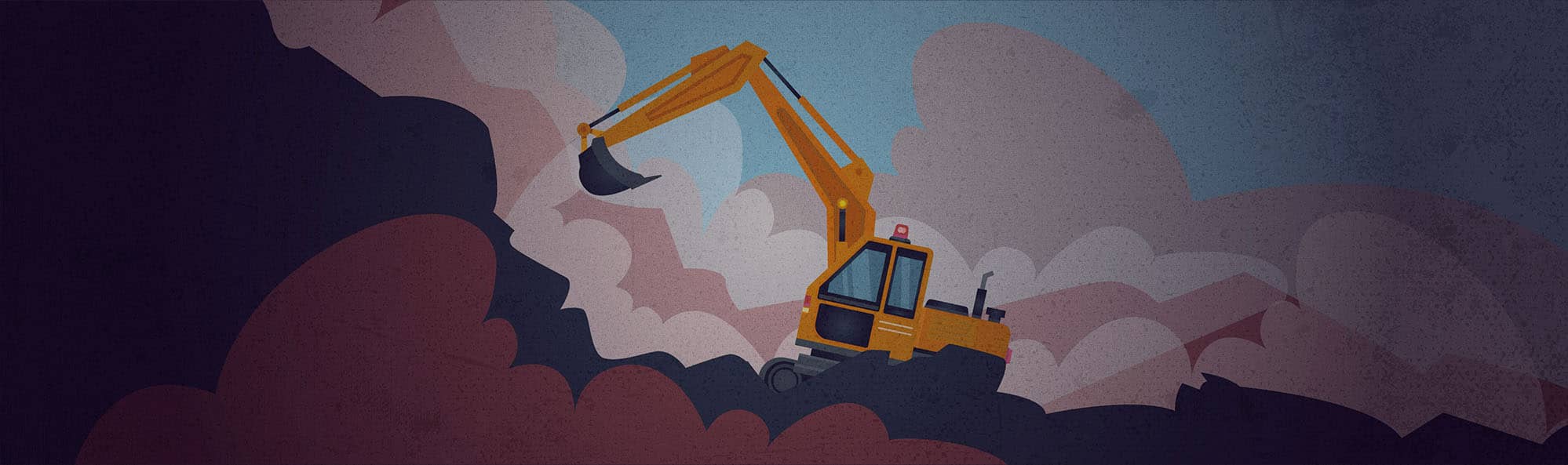
If you follow our blog at all, you know we write a lot about trucks. And while big rigs are a huge and recognizable part of the diesel industry—arguably the most recognizable part—they’re far from the only diesel machines out there. There is, in fact, a whole world of heavy-duty equipment out there.
I know that, Fullbay, you may be saying. Just play along. We’ve got to introduce things somehow.
You can find heavy-duty diesel equipment everywhere you look. Are there any construction sites in your area? Excavators, cranes, pavers, and graders all need maintenance and repairs at some point or another. Ever passed a mining operation and marveled at its size? These sites require their own diggers, trucks, and other types of equipment.
You can see where we’re going with this—heavy-duty equipment repair is a critical part of our construction and economic infrastructure, and much like the rest of diesel, it’s suffering from a dearth of technicians.
To get to know a little more about this field, we spoke to Matt Bean, owner and operator of Equipment Management Solutions and founder of HeavyTechs.com. He helped us understand some of the differences between truck repair and heavy equipment repair, as well was what the field is like and what kind of job sites an equipment tech might expect to find.
Ready for some real heavy metal? Let’s go!
ALWAYS ON THE MOVE
One of the biggest differences between a heavy equipment tech and their truck-repairing counterpart is that the heavy equipment techs are constantly on the road.
Have you ever seen some of the machines scattered around a construction site? They’re huge. Yes, a lot of the basic work is similar, but a lot of heavy repairs are done in the field. “Everything is so big and expensive to move, and they really can’t haul it to the shop because it has a blown hose, or the AC isn’t working, or things like that,” Matt says.
Maybe you can physically jam them into a repair bay, but getting them from Point A to Point B—especially if they’re not moving under their own power—is a tall order. So most heavy-duty techs pack their gear and head out to the site in their trucks. When that job wraps, they head to another, and then another. This constant movement has led to them being referred to as “mercenary mechanics,” which is totally my new band name.
(Editor’s Note: Suz doesn’t have a band.)
THE RULES CHANGE WITH THE JOB
Like much of the diesel field, heavy-duty equipment repair doesn’t have a ton of required certifications. But the sites you’ll work on as a heavy equipment tech are often filled with rules and regs to follow.
If, for example, you land on a coal mining site, you need to get their MSHA training (that’s Mine Safety & Health Administration), which is “basically OSHA for the mines.” It requires a 30-hour course that, upon passing, sets the tech up for life…but they do need periodic refresher courses. All that training needs to be set before heading to a mine site. However, each mine site has its own additional training they must undergo before working there.
(This is important stuff, by the way—it covers blasting safety, among other things. This is not training you want to skip.)
That sounds like a lot of rules and regulations, but rest assured that not every site is like that. The mines are a specific hazard; places like wind farms and verticals like civil engineering are more relaxed.
A SEASONAL JOB
Matt operates out of Montana, which, as you know, has real seasons. “Heavy equipment hates cold weather,” he says. Work can shut down for months at a time in states that have seasons. But once the weather is agreeable, all that machinery gets hauled out to a work site and “pretty much left there” until inclement weather means they have to shut down work for the season.
When asked what sort of malfunctions and problems a big machine might have, Matt was quick to answer: emissions and operator mistakes.
“80% of what people repair every day is related to emissions failures,” he tells us. Heavy machinery is somewhat behind the trucking industry in that regard, and is starting to catch up as far as emissions monitoring is concerned. “As more and more of the heavy equipment has emissions modules installed, we see more and more of these problems.”
He has also seen damage to heavy equipment caused by poor preventive maintenance, or a lack of preventive maintenance entirely.
SHOP LAYOUT
The shops are also built differently. As you might imagine, they’re bigger overall, and have bigger doors (all the better to fit machinery through). There are typically no lifts or pits (both standard features in a truck repair shop).
Instead, most equipment shops have overhead cranes.
“All the components you end up servicing are too heavy to lift by hand,” Matt tells us. “So you have these big gantry cranes overhead … they can lift anything from an engine to the tires—they’re too big to deal with—everything’s too big.”
And yes, the mobile repair trucks that head out to job sites are outfitted with cranes, too. Without them, technicians wouldn’t be able to get a lot of their work done.
Does working with these cranes require additional certification? Not usually. The National Commission for the Certification of Crane Operators requires certification for those operating cranes that can lift more than 2,000 pounds. If you’re lifting under that amount, you can get on-the-job training but don’t need to apply for additional certifications.
THE SATISFACTION OF A JOB WELL-DONE
So, what kind of personality might be drawn to heavy equipment repair?
In Matt’s experience, he hasn’t seen a lot of people jump from a career in heavy-duty trucks to one in heavy equipment, though he’s sure it happens. For the most part, though, they’ve started in heavy equipment and stayed there. Many of the heavy techs he knows have gone from school to dealerships. Others have started out working for contractors, often as oilers (a preventive maintenance technician who fuels/lubes/changes oil on-site) and work their way up into the mechanic role.
The ones Matt has known love taking things apart and putting them back together. “Repairing things is very satisfying to them,” he says, “They can see it and they can feel it.” A heavy-duty repair—fixing a giant machine and getting it back to work—is a visible, often obvious accomplishment that “really gets their dopamine going.”
GETTING STARTED
Now, we mentioned earlier that the heavy equipment field is suffering from the same technician shortage as the rest of the field.
The problem is getting started.
“People are intimidated,” Matt says. “They don’t know where to start.”
It also tends to be really hard physical labor, often in all kinds of weather. That means working in the blistering sun, a crazy downpour, or worse. Forget coming home splattered with oil or grease; you might well finish a long shift covered in mud, too. “It’s not very glorious,” Matt says, “but the pay is pretty good.”
Most of the heavy techs he’s known spend up to 10 years at a dealership, learning the ropes and getting the training they need to strike out on their own or with a partner. And once they actually get inside one of these giant machines, they may find they’re easier to work on. “There’s a lot more room in there,” he reports. “That’s one of my favorite things about working on bigger machinery.”
Heavy equipment techs tend to shoot for about 12 hours a day, at least in seasonal areas—you’re trying to crank out as much work as possible while the weather allows it. It’s often a short season, remember, and you’re factoring in travel time, often to remote or semi-remote sites. Matt did note that he sees physical repair shops fill up during the winter months (again, in Montana), as companies are trying to get everything in order during their downtime.
TO THE FUTURE…AND BEYOND!
How does the future of diesel equipment look?
Pretty heavy.
(Sorry, not sorry.)
Everybody’s short-handed, and hiring techs remains a challenge. Ever-changing regulations makes it challenging to keep up. But the industry isn’t going anywhere. The fields we’ve discussed in this article—energy, construction, civil engineering, and others—aren’t going anywhere. If anything, they’re going to expand even more as the country updates infrastructure and builds outward and sometimes upward.
In short, there’s room to grow. There’s certainly plenty of work.
With that said, finding said work can be a bit of a challenge. Matt realized this was not a problem you could solve with a LinkedIn group and eventually founded HeavyTechs.com, a first-of-its-kind platform that connects heavy-duty professionals with high-paying, high-quality jobs. “It’s a place for these guys to talk about their training and experience, so they can find good jobs and good people to work for.”
So go ahead and check out the site. And next time you pass a grader or an excavator or whatever this thing is, remember that there’s hard-working technicians keeping it running so it can do its job. It’s tough work, but well worth it!