Turning Wrenches
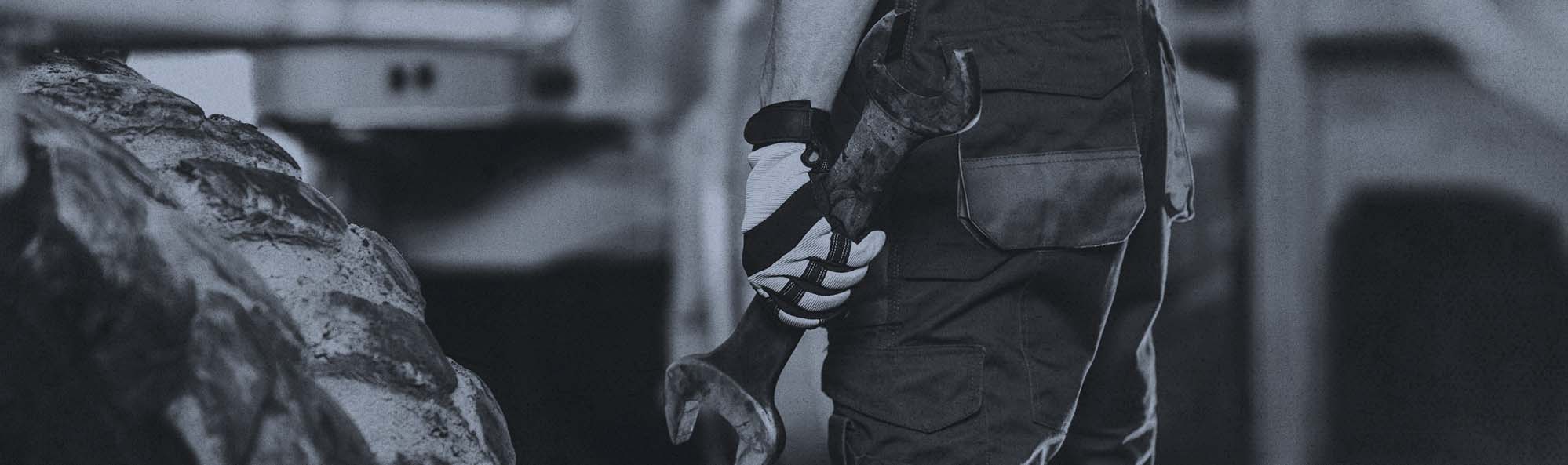
Business profitability relies on efficiently using resources and, in the world of heavy-duty repair, talented technicians are the resources. Skilled techs are the ones who provide the service that gives your shop its reputation. They’re masters at their job and know how to perform every little task deftly. However, many of those little tasks eat up time and get in the way of your shop’s efficiency. It’s a better use of their time and your resources to utilize techs for turning wrenches instead of saddling them with busywork. Delegate the simple, tedious tasks to an apprentice or other staff, and provide master technicians with the tools they need. These two simple steps free up lead techs to do the specialty work you hired them for.
Turning Wrenches Should be the Skilled Tech’s Focus
The billable hours a skilled tech can put in at your shop make up your labor inventory. It’s a large part of the service side of your product. Their time is money. That’s why having them perform basic tasks is like tripping over dollars to save pennies. Every 5, 10, or 15 minutes they spend on menial chores takes time away from turning wrenches, doing the advanced diagnostics and repairs that they’ve been trained to do. The result is that jobs take longer, reducing the number of them your shop can complete in a day and limiting your shop’s profitability.
Delegating to an Assistant and Others
Experienced techs have more time for turning wrenches when they delegate simpler tasks to diesel tech assistants. Many shops hire them on as apprentices to support the master technicians. They work closely with the more experienced techs providing necessary help. Some assistants’ duties include cleaning workstations and making sure the proper tools for the job on deck are on hand. They may also perform oil changes, replace belts, or finish up a maintenance or repair job after the complicated work is done. With limited experience, assistants’ pay is less than master techs’ but it’s still an expense. The money is well worth it, though, when it frees up lead techs’ time and allows them to complete more jobs each week. Other tasks can be successfully delegated to support staff, like service writers, parts managers, and office personnel.
Giving Techs the Tools They Need
Supplying techs with the right tools for the job doesn’t stop with sockets, screwdrivers, and wrenches. A large part of their job is keeping thorough, easy to read vehicle and customer records. Although important for shop use as well as customer convenience, it’s another tedious task that can get in the way of turning wrenches. In an effort to save time, many shops have computerized their record-keeping systems. In the process, they’ve discovered that the best heavy-duty repair software programs do more than just manage vehicle records.
Fullbay, for example, does a stellar job of maintaining details on individual vehicles, creating a sort of medical history for every truck that passes through your shop. But that’s just one of its useful features. Fullbay also schedules jobs, tracks inventory, orders parts, and you can use it to create estimates and invoices, too. Because Fullbay lives in the Cloud, you can run your shop from anywhere and check in on it anytime. And the customer portal is the icing on the cake, giving your customers not only access to their vehicles’ histories but also the ability to submit repair requests and pay invoices instantly. When the goal is getting techs back to turning wrenches, Fullbay is a vital tool that maximizes your techs’ valuable time. Fill in your info below to see how much more efficient and profitable your shop can be with Fullbay.