Partner Spotlight: All About the Technology & Maintenance Council (TMC)
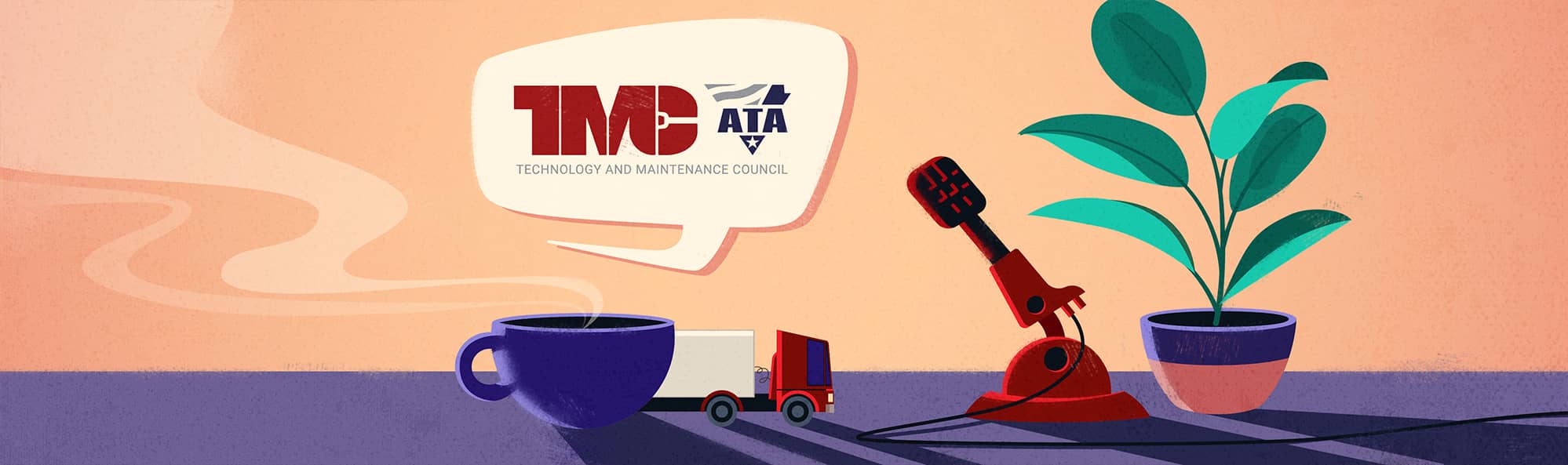
If you’re a repair shop owner, you should know about TMC.
No, not the movie channel, although you can put that on after you read this article.
We’re talking about the American Trucking Association’s Technology & Maintenance Council, cleverly acronym’d as ATA/TMC. They’re a cross-sections of fleets, equipment suppliers, educators, service providers, technicians, academia, owner-operators, and other stakeholders that collaborate to address the technology and maintenance issues impacting truck fleets.
“People have a vague idea of us sometimes,” says Executive Director Robert Braswell, “but they don’t know exactly what we do.”
What they do is live by their motto: Turning experience into practice. In other words, they’re an industry-wide effort to keep trucks and everyone around them safe.
We’re big fans of TMC; after all, we partnered with them to produce and release our State of Heavy-Duty Repair report. But as we put together that report, we realized a number of repair shops weren’t fully aware of what TMC was, or how much of its work has focused on individual service providers.
That’s why we sat down with Robert to find out more about TMC, its history, and which of its Recommended Practices (RPs) are built specifically for repair shops.
THE EVOLUTION OF RECOMMENDED PRACTICES
TMC has been around in some shape or form since 1956, though it wasn’t always known by that name. It began, Robert tells us, as a maintenance committee of the Regular Common Carrier Conference (RCCC).
In 1979, that group approached the American Trucking Association and reformed underneath them as The Maintenance Council. A few name changes later, and they emerged under the moniker they’re known as today. After decades of participation in the trucking industry, TMC has become a trusted source of industry standards for the fleets, OEMs, and component suppliers that utilize their RPs, which have become an industry standard.
But how are these RPs developed?
The need for an industry-wide collaborative effort became evident in the 1950s and early ’60s, when the forerunners of today’s RP study groups engaged in decidedly less cordial interactions. In short, truck manufacturing reps would join meetings of fleet managers and basically get torn apart. Robert describes these original meetings as “Shooting Fish in a Barrel Nights.”
The discontent arose from the efforts to build the nation’s highway system; the trucks they were using to do this were not up to the task, and manufacturers did not seem to be making a dedicated effort to improve them.
Over time, the tone shifted away from confrontation and toward collaboration, aiming to work together with manufacturers to improve the equipment. They formed study groups, which broke a vehicle into manageable pieces like tires, chassis, trailers, and so forth; these groups focused intensely on their particular area to determine the right kind of maintenance and operation. For example, one of the first things they addressed was, “How should an alternator be specified on a vehicle, and how should it be mounted?”
These early groups published their first recommended practices manual in 1973. That collaborative effort has continued into the 21st century, and the resulting recommended practices serve as general guidelines for manufacturers, fleet managers, and suppliers.
Because they are developed by consensus, and not just one person, every stakeholder gets a say. No one has to adhere to them, but rather they act as a sort of code of honor. If you’ll forgive us shortening it up even more, if your work and components are compliant with TMC’s recommended practices, people know you’re “a good egg.”
It generally takes about 18 months to two years to come up with a recommended practice. Once a practice has been created, TMC usually looks at it again every five years to keep up with changing technology. An exception to this is the RPs related to software, as programming is constantly changing.
HOW CAN WORKING WITH TMC HELP MY SHOP?
Sure, fleets love TMC and its RPs, but did you know that it’s built a lot of recommended practices around better repair shop operations?
These RPs are built around two critical parts of running a shop:
- Better educating a service provider to the needs of a customer
- Helping that service provider show customers they know what they’re doing
Robert notes that one of the biggest problems with third-party repair orders is communication. Everyone wants to sync up differently: through email, by voice, by text, and so on. RP 535 emerged to help resolve this; it is a template for building relationships between fleets and service providers.
If you’ve already got a method for developing relationships with your customers, great! But if you’re just starting out, or want to do some fine-tuning of your own process, the RP will steer you in the correct direction.
To that end, there are almost 20 RPs that will specifically help repair shops run better.
- Measuring customer satisfaction
- Workflow issues
- Rapid repair issues
- Career development
- Conflict resolution
- Quality control
- Managing difficult customers
- Parts acquisition
- Mentoring
In short, these RPs provide an absolute wealth of information for the independent shop owner.
Once you’re a member, you can get your hands on these RPs in several ways. Do you want a 4,000-page book (in a three-volume set) that will look impressive on your desk and show everyone that you know your stuff? They’ve got it. Would you rather access RPs online or on your smartphone? You can do that, too.
And people who love CDs—there are a few of us still out there—TMC hasn’t forgotten about you. You can obtain the collection on future coasters, too.
PARTNERING WITH TMC
TMC is all about helping the industry be the best version of itself, so it’s no wonder the crew here at Fullbay likes them so much.
We also aim to help repair shops and the diesel industry improve and thrive in the coming years. That’s why we’ve partnered with them—and why we can offer Fullbay subscribers a special rate. You can save $50 on your membership by clicking here and using the promo code TMCFULLBAY21. You can put their experience to work for you in no time at all—just tell them Fullbay sent you!