Heavy Duty Parts Inventory
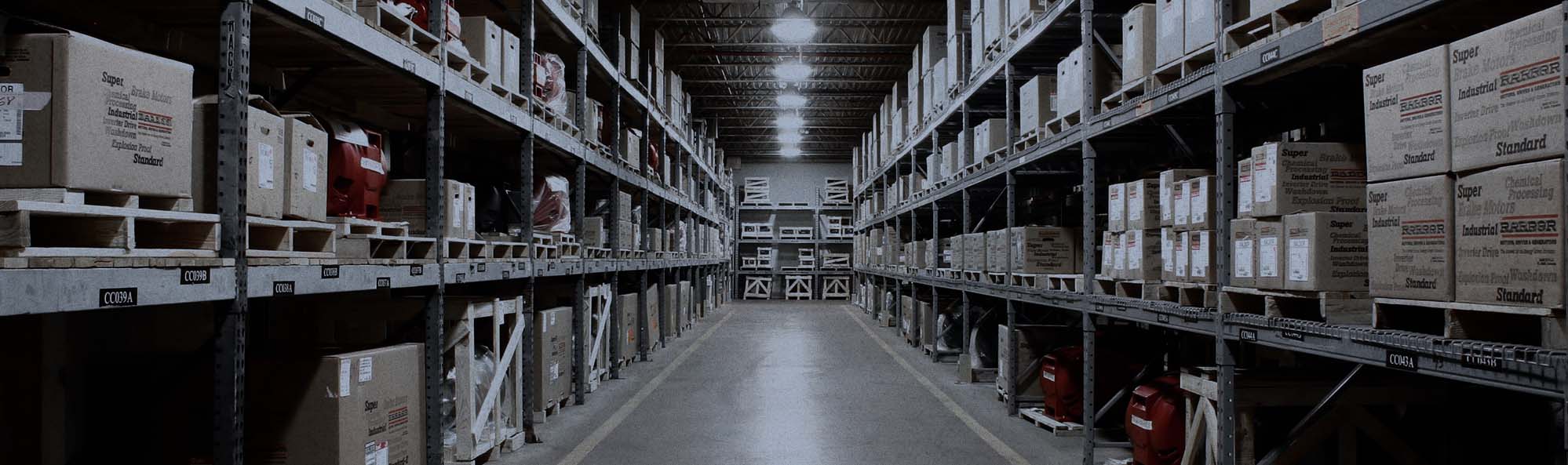
Imagine you had a pallet of cash sitting in your shop. Would that keep you up at night? Would you worry it might slowly walk out the door? What would you do to protect it? Well, your heavy duty parts inventory is basically like having a pile of cash sitting around. It needs to be tracked, and reconcile just like any other bank account.
Most shops do not actively track their heavy duty parts inventory. It’s one more thing to do, and running a shop can be so hectic, owners either consider lost inventory a cost of doing business, or they just try not to think about it.
The reality is that not tracking your heavy duty parts inventory can be a massive cash drain on your business.
Consider this: Say your overall shop margin is 35%, where it should be. Now say you lose $300 a month in inventory, whether it is lost, damaged, or walks out the door. In order to make up that $300, you don’t go out and do a $300 job. You would have to do a $857 job just to recoup your monthly loss.
Since most shops we meet are well below 35% (that goes up fast when you start using Fullbay), that number skyrockets. For example, if your shop margin is 10%, you would need to do a $3,000 job every month just to make up for the loss on your heavy duty parts inventory.
So are there any common sense things to do to avoid these kinds of losses? We recommend three: secure your inventory, do regular cycle counts, and reconcile the balance monthly.
Secure Your Heavy Duty Parts Inventory
Don’t tempt your employees. Studies show that otherwise honest people have been pulled into fraud from the sheer, overwhelming temptation of it. You may very well be surrounded by good, honest people. But making it easy to walk away with shop assets can actually pull people to the “dark side.”
Secure your heavy duty parts inventory as best you can. Obviously you need to be reasonable about it. But consider putting it behind a lockable door or gate, and pointing a camera at the area. Remove the temptation to steal, and your losses will go down.
Do Regular Cycle Counts
No one likes counting inventory. And counting everything? It’s so overwhelming, and you are so burned out by the end, that it’s no wonder most shops don’t do it. But have you considered cycle counting?
Use a software that allows you to track your parts by location, like a certain shelf, or a certain service truck. This breaks your inventory into bite-size chunks that can actually be counted fairly easily. This is called “cycle counting.”
Consider cycle counting your inventory once a week. Take 30-45 minutes to double check your stock. Not only does this help identify theft early, it also helps you get to know exactly what you are carrying, whether you have too many of certain parts, and whether you are running out of others.
Reconcile Like It’s a Bank Account
Reconcile your heavy duty parts inventory like it’s a bank account, because it basically is. Whatever system you are using, run a report showing your inventory balance at the end of every month. Then reconcile that to your balance sheet, exactly like you do with your bank accounts. (You ARE reconciling your bank accounts right?!)
It’s inevitable for weird things to pop up in your inventory transactions. Reconciling every month helps you catch those, deal with them, and keep a clean balance. It also gives you a clear view into how big that pile of cash sitting out there is. The higher the inventory balance, the higher the carrying cost.
Learn More
Take heart that you aren’t the only one who doesn’t like tracking inventory–a majority of your fellow shop owners don’t even bother. But tracking and protecting your heavy duty parts inventory will save you a lot of money and heartache in the long run.