Four Signs You Need to Hire a Parts Person
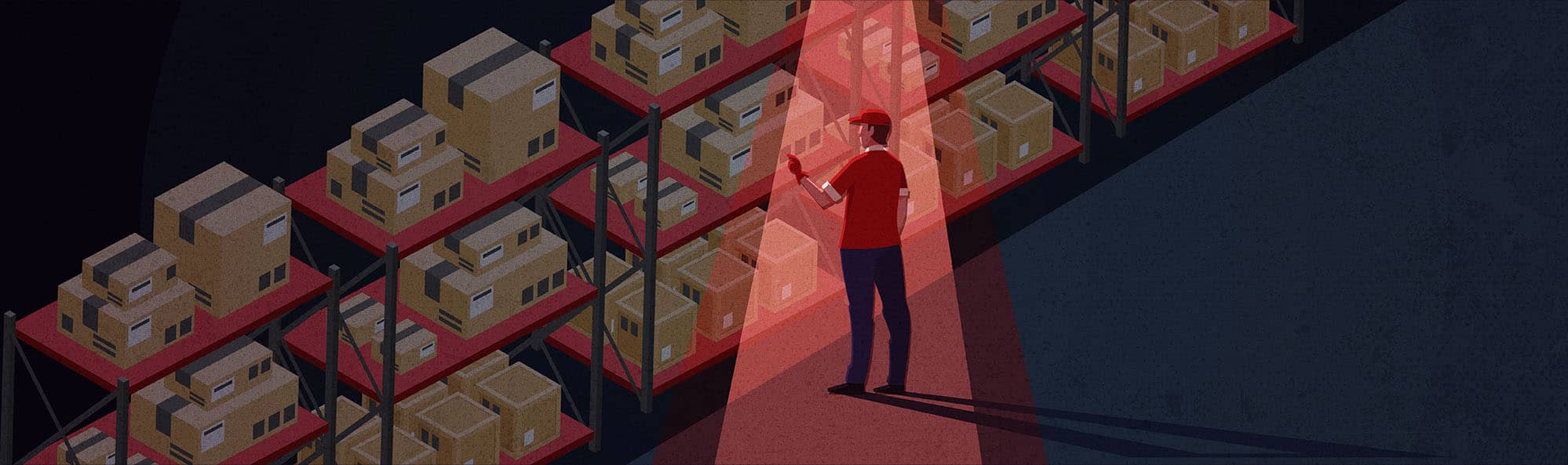
There comes a time in every repair shop’s life where its owner must make a critical decision: pizza or burgers?
This is not an article about either of those things, although we’ve succeeded in making ourselves hungry, so thanks for that.
(Editor’s Note: You brought that on yourself, Suz.)
True. So instead of sitting here fantasizing about dinner, we’re going to focus on the other important part of growing your operation: hiring a full-time parts person.
Don’t be silly, Fulbay, you might be saying. I’m a one-man band/I only have two techs/my dog fetches my parts/I don’t need a parts person.
And look—maybe you don’t. Here, we’ll bold it so you know we’re serious:
Not everyone needs to hire a parts person.
But some shops do need a parts person. This article is for them.
Do any of these scenarios sound familiar?
- You (and/or your techs) are losing tons of time running down parts
- You’re losing income running down parts
- Inventory is missing or rotting on the shelves
These are all indications that a parts person would help, rather than hinder, your operation.
That still doesn’t mean you have to hire. You may not want to. You may not be in a position to. Your dog might not want to share duties.
For now, let’s talk about how a parts person can ease the problems described above—and what else they can bring to the shop.
YOU NEED A PARTS PERSON IF…
How badly you need someone to deal with parts is going to depend on your existing workflow.
If you have processes in place (Fullbay can help you with those, by the way), you can possibly put off hiring someone to handle your parts. But let’s look at the three examples we provided in the beginning of this article
Your techs are running down parts. Your techs should be in the bay (or in their trucks), turning wrenches and getting work done. If they’re roaming back and forth between the parts room, or driving all over town to find a part…that’s a waste of their time and a loss of productivity and revenue.
Zeb Todd, parts manager at The Service Company, has seen some situations get pretty hairy. “When people can’t do their assigned jobs, or multiple people are doing the same job—like the techs and service writer are both ordering parts—it’s time for a dedicated parts person,” he says.
If you’re reading this paragraph and wavering on the idea, look into your techs’ efficiency and productivity. Zeb says that’s a good indicator of whether you have “the right amount of people in the right seats.”
(If you’re not using Fullbay and don’t have a way to easily track tech efficiency, you can try this more hands-on method: take note of how many minutes (or hours) per day a tech spends messing with parts. That’s a loss in time that they can’t work and you can’t bill.)
You’re running down parts. Dude, you should be either running the business or wrenching yourself, not attempting to track down a new turbo or set of brake pads. All the problems associated with techs and service managers chasing parts applies to you, too!
You’re losing income running down parts. We don’t just mean losing the revenue associated with technicians leaving the bay to rummage through the parts bin. We also mean the haphazard ordering and stocking that can go on if you don’t have a detail-oriented parts person overseeing things.
“A parts manager should help the company grow by reducing expenses through good core management and practices and return policies,” Zeb tells us. They’re also the dark masters of strategic buying, ordering, and vendor negotiation.
Something else to consider: if you have 13 people chasing parts, you will probably be dealing with 13 different parts-sourcing styles. That sounds…complicated.
A professional parts manager will be able to look at your shop’s data and determine what needs to be kept stocked and what you can order as you need. Because if you’re just ordering inventory based on gut feeling or what you think you need…
Your income is rotting on the shelves. While it would be nice if unused parts remained crisp and perfect for all eternity, the reality is everything has some kind of lifespan. If you spent thousands on hoses and they’re hanging on your wall for over a year, figure at least 20% of that investment will dry out before you can use it. Worse, it might seem fine, end up installed, and some driver only gets about a thousand miles out of it before it blows.
That’s sadly called a comeback repair.
HOW FULLBAY CAN HELP
C’mon, you knew this part was coming!
While we can do many things, we can’t hire a parts person for you. But we can help a shop get their inventory in order and see where parts are coming and going. The inventory velocity report shows you how fast parts are selling, and whether you’re stocking too much or too little. The inventory reconciliation report is like a bank statement for your parts room.
And that’s just two of many!
In short, Fullbay can help you get your parts room in order…and if you’ve already got a parts manager, we can help them run a tighter ship.