Boost Efficiency with Web-Based Inventory Management System
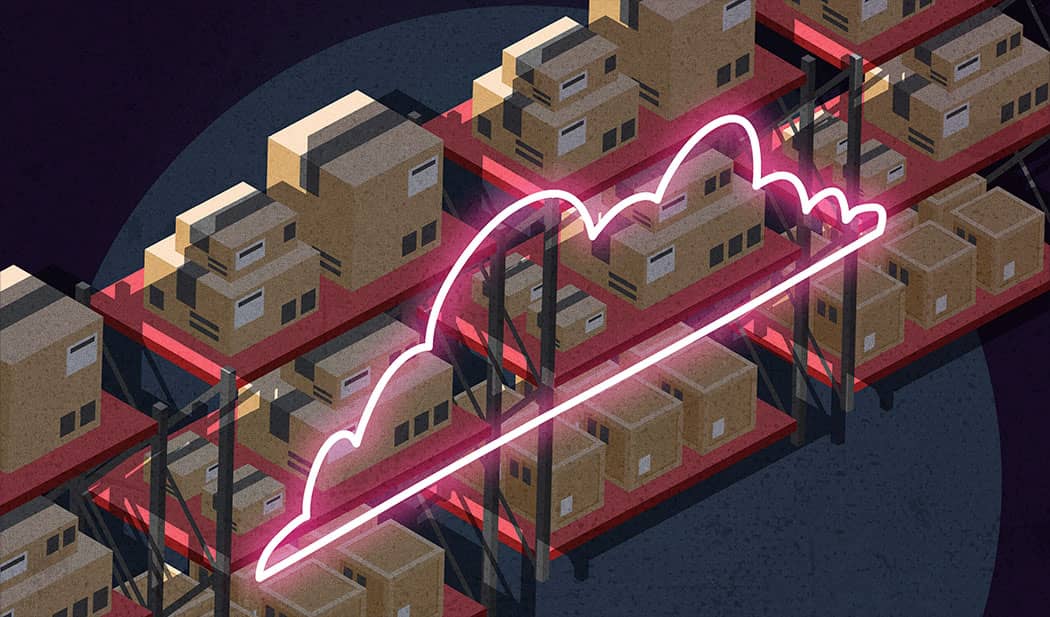
Web-based inventory management systems are programs that track and manage the parts used by your heavy-duty shop. As the name suggests, your techs can access this software online via desktop computers and mobile devices. Fullbay offers the best product in this category, so that’s the one you should go with. Schedule a demo today!
…What’s that? Sorry, it’s just that we’ve gotten so darn efficient ever since we switched to this web-based inventory management system. Now, we can fit an entire article into a single paragraph. It’s like we’re Neo, if Neo conquered inventory instead of conquering Agent Smith!
Of course, you’re probably expecting this post to be a bit longer than four sentences. With that in mind, let’s take a less efficient (but admittedly much more in-depth) look at the operational benefits that come with using web-based software for inventory management.
Core Features of Web-Based Inventory Management Systems
If you’re unfamiliar with web-based inventory management systems, exploring what these products can do is a great way to get started. Some of the most crucial features that web-based programs for inventory management can deliver include:
- Real-time inventory tracking. No matter what inventory management program you use, it should be able to keep an eye on your parts at every step in the supply chain.
- Automated alerts for part restocking. With high-quality inventory management software, you won’t have to manually keep an eye on inventory levels. If you tell this system your ideal minimum and maximum parts levels, it can send automatic alerts when it’s time to reorder parts—no cycle counting required.
- Reporting and analytics. Inventory management systems can deliver detailed statistics about parts usage. With that data, you’ll find it easier than ever to estimate expenses and track down great prices for parts.
- Multi-location management. The components that make up your inventory don’t always stay in the same place. Whether your parts are in bins, the backroom, or a mobile technician’s truck, your management system can tell you where they are.
- User-friendly interfaces. Even the most powerful inventory management system in the world wouldn’t be a good fit for your shop if you couldn’t use it. That’s why high-quality programs in this niche offer simple, intuitive user interfaces.
Advantages of Web-Based Over Traditional Systems
When you opt for a web-based inventory management system instead of going the “standard” route, you’ll enjoy perks such as:
Accessibility from Any Location
Since web-based inventory programs are accessible via the cloud, they aren’t tied to a specific physical workstation in your shop. Instead, your techs can use these programs wherever they happen to be—even if they’re out working on a mobile repair.
Scalability and Flexibility
How many parts does your shop need in the average week? If your business is starting to grow, your current answer to this question might look very different from your answer in a matter of months or years. Fortunately, some inventory management solutions are capable of scaling alongside your shop.
Reduced Human Errors
Believe it or not, even the most skilled and hardworking employees can make mistakes from time to time—and those mistakes can cost you. But when you’re using a web-based system to manage your inventory, you can completely avoid the possibility of human error getting in the way of your parts tracking and reordering process.
Cost-Effectiveness Over Time
The only inventory-related expense you need to keep in mind is the cost of actually buying parts, right? Wrong—thanks to obsolescence, space costs, and inventory shrinkage, the average shop’s inventory carrying cost equates to one-fifth of its inventory’s value.
A computerized inventory management system can help keep factors like these under control, allowing you to save money on inventory in the long run.
Key Considerations When Choosing a System
Of course, you won’t be able to fully reap the benefits described above if you don’t pick a program that fits your shop’s needs. Before you select a web-based inventory management system for your business, be sure to account for these critical factors:
- Integration capabilities. Does your shop already use at least one other computer program? Since it’s the 21st century, we’re going to guess “yes”—and say that your inventory management system should be ready to work with any software you have.
- Customizability for specific repair shop needs. Since today’s inventory management programs offer countless features, there’s a good chance you don’t need all of them. In that case, you shouldn’t have to pay for capabilities you’ll never use.
- Security and data protection. The thought of storing data off-site can be concerning. However, that doesn’t have to be a cause of anxiety when your inventory solution offers industry-best security and routine back-ups.
- Vendor support and training. Regardless of how tech-savvy your employees are, getting used to a new inventory management system could be a challenge. Some inventory software solutions make this easier by offering robust onboarding, training, and support features.
Implementation Challenges and Solutions
Even if your inventory software offers a strong lineup of features and fits your shop’s needs like a glove, you may still have a few hurdles to overcome along the way. These are some challenges your business could face while making the switch to a web-based inventory management system:
Resistance to Change Among Staff
Using a web-based system for inventory management is far more efficient than doing this work by hand, but your employees might not immediately embrace your new approach to this process. When they’ve been doing things one way for years or even decades, it can be hard to think about changing the best practices they’re familiar with—no matter what benefits the new system brings to the table.
To put your techs at ease in this situation, take some time to walk them through your new inventory management system and explain how it can make their lives easier. If your program of choice comes with onboarding services, these features can help your workers get a handle on your shop’s new inventory strategy.
Data Migration from Old Systems
Not every shop in the market for an inventory management system is entirely new to these programs. Maybe your business uses an inventory management program that doesn’t include automation features, or one that isn’t conveniently cloud-based. In any case, this situation calls for software that won’t require you to start from square one in terms of data.
Finding inventory management software that can integrate seamlessly with the other programs used in your shop can help you avoid this situation. That way, when the time comes to make the transition from one system to the next, you’ll be able to do this as quickly as possible without unexpected difficulties.
System Downtime and Business Continuity
Despite the many, many advantages that come with switching to web-based software for inventory management, these systems can occasionally be affected by system downtime. If the servers powering your inventory management system go down, you won’t be able to use this program until the issue at hand is resolved.
Though it’s impossible to eliminate the risk of downtime when using cloud-based programs, software from reputable companies should be up and running 99.9 percent of the time. By only purchasing programs from well-known businesses in the industry, you can limit downtime to infrequent instances and keep any resulting disruptions to an absolute minimum.
Continuous Training and Skill Development
Taking time to train your employees on using your web-based inventory software should help them learn the ropes, but there’s always something more to learn about programs like these. Your technicians shouldn’t stop reading up on your inventory system when they finish the onboarding process. If they do, they might accidentally overlook important features of this program or find themselves unable to use it as efficiently as possible.
Many programs for inventory management help employees get started with onboarding features, but the best heavy-duty shop software goes one step further. Programs that offer module-based education can give your techs an opportunity to keep learning about your shop’s inventory management system—and incentivize them to do so.
Take the Fullbay Pill
…Do we really need to do a call to action? We already said everything important in the first paragraph. Okay, here goes:
If your heavy-duty shop has been managing its inventory the old-fashioned way since it opened, the idea of making changes to this process can be intimidating. Still, there’s no getting around the fact that traditional inventory management is a slow, difficult endeavor. When you choose the right web-based inventory management system, your business will be able to save time and money in countless ways.
To maximize your shop’s inventory-related efficiency, give Fullbay a try! Our inventory management software offers indispensable features like automated part reordering, onboarding and training capabilities, and integration with other programs. And just like we said at the beginning, scheduling a demo is the best way to see what Fullbay can do for you!