Benefits of an Automated Inventory Management System
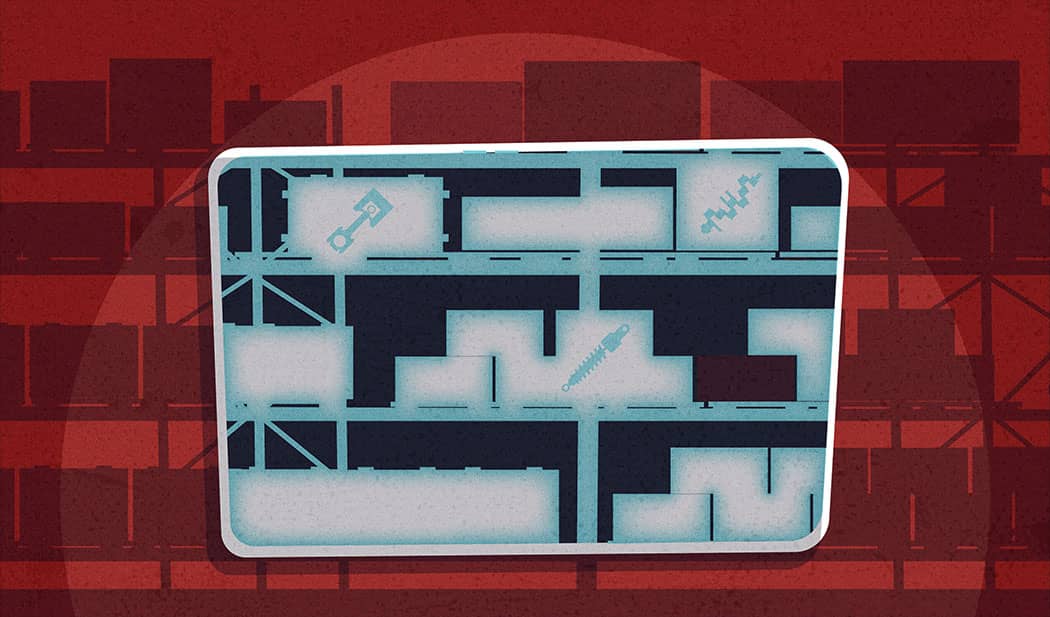
Here’s a short story for you. Once upon a time, someone said, “Wow, we have a lot of inventory. We need a way to manage it.” And inventory management systems were born.
Some time later, those inventory management systems went digital and gained automation capabilities—making them faster, more efficient, and more profitable for heavy-duty repair shops. Not everyone switched to automated systems, but those who did lived happily ever after. The end.
(Pretty good story, right? We even got it published on this blog.)
Using inventory management systems to track and order parts can deliver some serious perks. If you’re still relying on manual parts management, even following best practices can’t truly bring your heavy-duty shop’s inventory strategy into the 21st century. Instead, take the next step with Fullbay’s complete guide to the merits of using an automated system for this process.
Understanding Automated Inventory Management
Inventory management systems aren’t too difficult to understand—this term refers to programs designed to help heavy-duty shops keep an eye on the parts they have in stock. Thus, the term “automated inventory management system” describes software that automatically handles tasks related to managing inventory.
Manual inventory management systems require employees to keep track of part levels, financial data, and more. Of course, that takes up valuable time these workers could have spent completing repairs or other related tasks. Furthermore, human data entry is highly prone to error—if your stock numbers aren’t accurate, you could be unpleasantly surprised when it’s time to complete what should have been a quick and easy job.
With an automated approach to inventory management, you won’t have to worry about any of these issues. Systems in this category are capable of tracking the parts you have in stock, monitoring what’s coming in and out of the shop, and eliminating a major distraction for your staff. You’ll still have to cycle count and establish an accurate system for counting parts when they first arrive, but while using an automated system for your inventory management needs, you can reduce the chance of human error.
Automated Inventory Management: Benefits You Should Know
Some of the biggest perks that automated inventory management systems bring to the table include:
Financial Benefits
It’s easy to assume that simply having inventory around doesn’t cost your shop anything. But that’s not the case—taking factors like obsolescence, space costs, and inventory shrinkage into account, carrying inventory costs auto and diesel shops about 20 percent of that inventory’s value each year.
Fortunately, the in-depth tracking offered by automated inventory management systems can mitigate this issue. By getting a clear picture of how much stock is actually being sold on a monthly or yearly basis, you’ll have a better idea of how much to order rather than just making a guess. This is huge for your shop’s cash flow.
Inventory management systems will also keep track of order history for you, which includes cost and vendor information. When it’s time to reorder, a parts manager can get good deals by quickly scanning through to see which vendor had the best price last time.
Operational Excellence
Performing regular cycle counts is a fact of life, but inventory management software can make it less of a hassle. By keeping an eye on which parts move the fastest (or slowest), you can schedule cycle counts accordingly. Rather than count your entire inventory every time, you can check the fast-moving parts more often and the slow-moving parts less often.
Automated inventory management software also helps shops manage stock levels. You can use these programs to set thresholds for the number of parts you want to keep in stock. When you’re running low, you can get an automatic alert so you know it’s time to restock!
Obviously, reordering parts involves a financial cost—but this process can cost you in terms of time, too. In the past, parts managers would have had to track down what to order, make a list, then order those components manually, taking them away from their work for a while. Though automated inventory management can’t eliminate the cost of parts, it can streamline your procurement process, helping you save time around your shop.
Enhancing Customer Service
Do you think adopting inventory management software for your shop would be a purely “under-the-hood” upgrade? Think again: automating your approach to inventory management can help you keep your customers happy in a few different ways.
For example, if you always know where your inventory is, you won’t need to look around for that one part—and eliminating this search process can drastically speed up your turnaround times on repairs. Better yet, automatic alerts when it’s time to reorder parts will significantly reduce your odds of needing to delay a job due to an out-of-stock component.
Empowering Employees
The technicians working at your heavy-duty shop already have a lot on their plates. With that in mind, you’ll want to make it as easy as possible for them to focus on their actual job duties—and inventory software can help.
With one of these programs, you can reduce the number of tasks these employees must handle manually. When they do need to manage parts, your workers will be able to take care of this quickly and conveniently by accessing your inventory software with a mobile device.
Thanks to these benefits and others, your shop’s techs and other employees will be significantly happier when you upgrade to an automated inventory management system. That should translate to reduced levels of burnout and greater job satisfaction among your workers.
Reporting
Some programs offering inventory management features also provide detailed reporting on inventory and other aspects of heavy-duty shops. With timely, accurate access to this information, you can analyze data on your business’ past performance and use that to make strategic decisions going forward.
For example, you can keep track of which parts you bought from which vendors and when you bought them. From there, you can better estimate your costs in the future—and maybe even spot trends around who offers the best prices.
Future-Proofing Your Business
Speaking of the future, the best programs for heavy-duty inventory management are ready for whatever comes next. Ideally, your program of choice can adapt to upcoming market changes without difficulty. And if you purchase another piece of software for your shop, there’s no need to worry—the best software in this niche can easily work alongside other industry-leading programs.
A highly scalable inventory program can also continue meeting your needs even if your business’ size—and its need for parts—increases significantly. The ability to add more users, customize your settings, and build tailored automations lets you focus on your shop’s success without worrying about how it will affect your parts procurement process.
Live Happily Ever After With Fullbay
By investing in an automated inventory management system, your heavy-duty shop can organize and streamline a lot of the work that goes into managing parts inventory—just to name the most obvious benefit. That’s a story we can all get behind. Still, some programs are better than others when it comes to helping shops save money, avoid unnecessary work, and fix their inventory. Fullbay is tailor-made for heavy-duty repair shops with specific tools and capabilities needed to manage a parts inventory, like tracking parts across multiple locations, setting inventory thresholds, getting order notifications, accessing in-depth tracking/reporting, and so much more. See for yourself and schedule your free demo