The Many Lives of a Fleet Manager
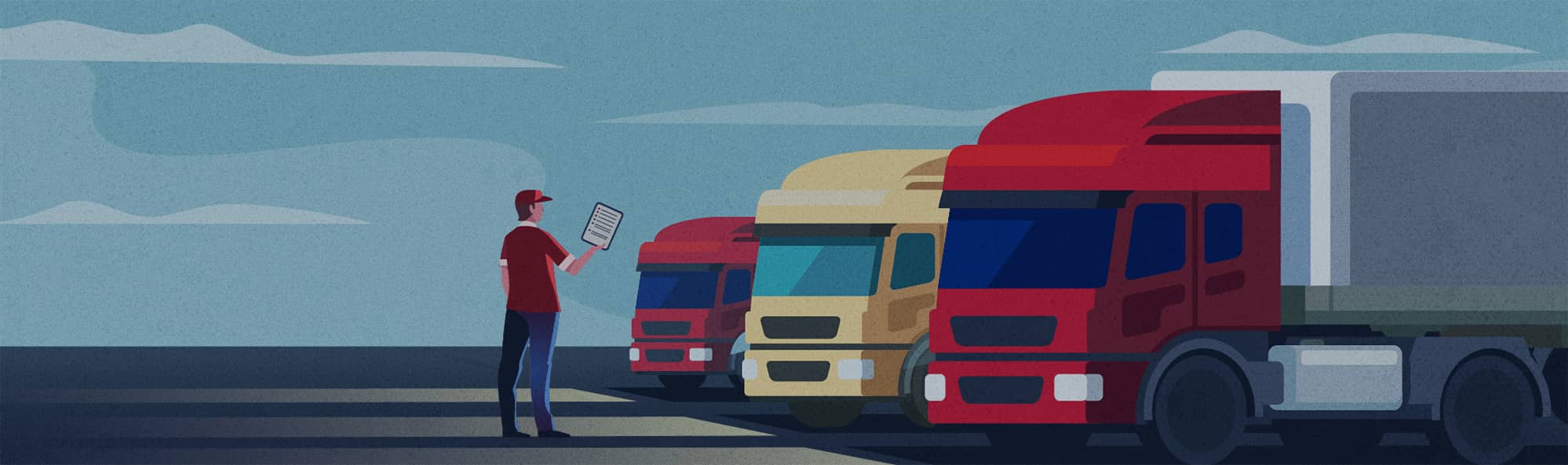
Ah, fleet managers. What would we do without them?
No, really: what would we do without them?
The answer is not much. The roads would be awash in chaos like some kind of Mad Max prequel.
We’ve talked a lot about various roles in repair shops: service managers, parts managers, technicians, and salespeople, among others. But for this article, let’s shift gears a bit and take a look at the people on the client side of things—namely, the fleet managers.
If you’re handling PM work for local fleets, odds are you chat with a fleet manager or two pretty frequently. While the smallest fleets might be able to contract with an outside service to handle their fleet management, generally speaking, most fleets over six trucks should have a person in charge of repair history, maintenance cycles, and so on.
Fleet management is a huge role, and each shop or company is going to put their own spin on it. Because the work varies so sharply, we decided against writing a straightforward “Day in the Life” article. Instead, we’ve compiled this list of duties we saw in both smaller fleets and larger, more corporate fleets.
We also spoke to a couple of people with particular experience in this field:
- Chris O’Brien, COO of Fullbay and former fleet manager of Shamrock Foods
- Robert Auer, fleet manager for UPS
So, whether you’re thinking about making a career change as a fleet manager or just want to know what your primary fleet contact does all day, this article is for you!
SAFETY AND UPTIME: TWO PARTS OF THE SAME WHOLE
Uptime is always the magic word, isn’t it? Any fleet manager wants a safe, reliable fleet on the road.
“A unit down is big money for us,” Robert says, “so trying to make sure we have no breakdowns is first and foremost, along with safety. They go hand in hand.”
Ultimately, anything mechanical is eventually going to break down. A fleet manager won’t just be ensuring trucks get their PMs covered; they’ll also be looking for trends in the hopes of finding potential problems and fixing them before they can become issues.
In a recent column, Fullbay co-founder and CEO Jacob Findlay talked about the grim equation behind the eleven heavy truck-related deaths per day. Improper maintenance is a large contributor to those deaths; if something fails while a truck is on the road, that truck can do a lot of damage to the vehicles and people around it.
So, what’s the best-case scenario for an improperly maintained truck? It winds up sitting in a repair bay getting fixed—instead of being out on the road making money. The worst-case scenario is that a vehicle contributes to the eleven daily deaths. Poor maintenance practices can be at the root of both.
Not surprisingly, fleet managers have a vested interest in making sure their vehicles are in good working order.
COST MANAGEMENT
It costs money to keep a fleet running. How many of these costs fall under the authority of the fleet manager will depend on the business itself, but they’ll often have a bottom line they need to meet, as well as a fixed amount they can spend on things like PMs and emergency repairs.
For example, a fleet manager who usually sends vehicles to an internal repair shop may still need to outsource things occasionally, and will have to work out costs for that. They’ll also need to know how much they can spend on parts, overtime, and fuel.
PEOPLE MANAGEMENT & BUILDING RELATIONSHIPS
Figuring out costs and safety measures alone sounds like a full-time job, but many fleet managers are also in charge of their respective departments. They’re often conducting meetings and overseeing the supervisors who oversee the technicians on the floor.
“We gotta watch out for all angles,” Robert says. “We’re managing a fleet, but also managing employees and assets, whether it’s parts inventory, vehicle inventory, and so on.”
This means helping others forge relationships, whether it’s through getting the staff together for a Friday Happy Hour or intervening when tempers get heated. “We’ve all heard the stories about drivers and technicians getting short with each other or squabbling over repairs,” Chris says, identifying those kinds of interactions as a quick ticket to Troublesville. The fleet manager has to make sure those relationships stay healthy, because, “An unhealthy relationship leads to unhealthy repairs and less uptime.”
A fleet manager is often also in charge of building and maintaining vendor relationships. Where do they send their trucks for PMs? Who handles their emergency repairs? If they’ve got an in-house repair shop, where are they sourcing parts?
While some fleets may parse those roles out to additional people, in many cases you’ll find fleet managers are the ones on the phone with a vendor, trying to ensure they get the part they need when they need it.
The fleet manager doesn’t just build a relationship and set it off to the side, either. They’re constantly re-evaluating what that vendor brings to the table. How soon are they bringing your parts? How many mistakes have they made? Are you getting a fair price, or are prices shooting up out of nowhere?
It’s a lot to keep track of.
TRACKING VEHICLES & SPECCING EQUIPMENT
Your average fleet manager also knows where every truck in the fleet is at any given moment. These days, they have some help with that through telematics, but there’s still a lot for them to look out for. They know where trucks are bound, what road conditions and bad weather may be ahead for those in certain regions, and whether they’re on schedule or behind.
But the job doesn’t stop there.
Many fleet managers are tasked with working with various transportation departments to make sure the vehicles their fleets operate are A-OK to operate where they need to. For example, if a fleet needs to do city driving, you can’t always run a semi truck trailer up and down the streets. Maybe you need box trucks or sprinter vans—or maybe you can pull off a tractor-trailer, but only on certain roads.
Part of the job is speccing a vehicle that has quality parts, or can hit a quarter-million miles, or meeting other strategic KPIs. This can get pretty complicated as a fleet manager attempts to outfit vehicles with equipment that will last. They may be constrained by vendors, which can mean they’ve got to spec their vehicles with a certain brand of tires or belts.
Pretty granular, right?
And it doesn’t stop there. Much like fleet managers are always re-evaluating vendor relationships, they’re often eyeing manufacturers, too. Just because they’ve had good luck with one brand doesn’t mean they can always buy that brand. Manufacturers sometimes change up their speccing or jack up their prices. Sometimes the fleet needs to carve money out of their budget to get what they need—and yep, you’ve got it, the fleet manager may end up handling that.
RETAINING RECORDS
No matter where your vehicles go, you need records of their maintenance and repairs, and you’ve got to keep those records going back at least a couple of years.
People can be held financially and legally responsible for repairs that are done (or not done) on vehicles. Chris has seen maintenance people named in lawsuits as the responsible party for negligence in not maintaining a piece of equipment.
To avoid this kind of trouble—and the accidents that can lead to it—fleet managers must keep their maintenance system and records absolutely airtight. Every day, they’re making sure the vehicles maintain federal compliance through safety inspections and basic wear and tear inspections and replacement programs.
They record everything that goes on with those vehicles. And they keep those records.
“If you did a brake job three months ago and there’s a fatality, you’re on the hook,” Chris says. “Was the brake job the reason for the accident, or was it not? They’re gonna go back to those records.”
A ROLE WITH MANY FACETS
Yes, fleet managers do a lot. But let’s bring things back around to safety, shall we?
Chris and Robert both talked a lot about safety. And why not? We’ve already covered how dangerous an improperly maintained truck can be. While a fleet manager does focus heavily on maximizing uptime for their vehicles, their number one priority is safety. A truck needs to be safe to drive, and it needs to be safe for those on the road with it.
If you read through this article and are now thinking, Good grief, Fullbay, fleet managers are busy people, well, you’re right. And odds are, if you’re a fleet manager reading this, you may be laughing: Fullbay, you have no idea.
So, fleet managers of the country, we salute you in all your varied roles! Thank you for staying on top of everything so the trucks in the supply chain run smoothly and safely for everyone involved.