How to Use Data in the Parts Purchasing Decision
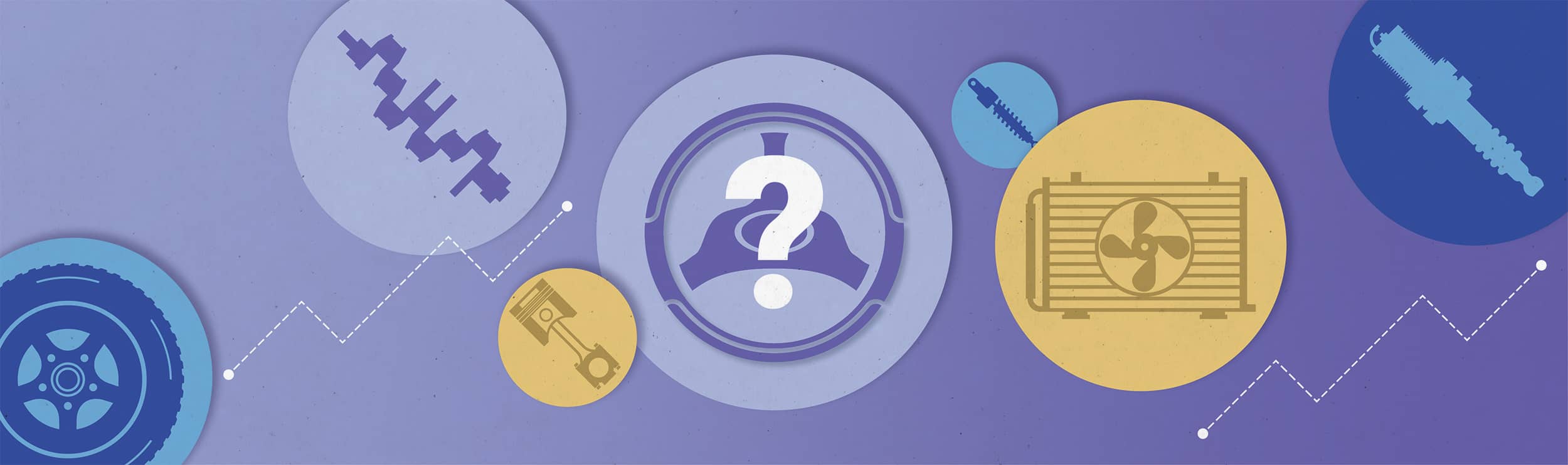
The proliferation of parts options can make it difficult to choose the right part for a vehicle. The right information can ensure you get the right parts at the right price.
Today there seems to be more options for truck and trailer maintenance and repair parts. In recent years, there has been a proliferation of private label parts, all-makes parts, price point parts, white box parts, will-fit parts, reman parts, rebuilt parts, factory replacement parts, aftermarket parts and, of course, genuine parts.
It has gotten rather confusing when it comes to deciding which part is the right one for completing a repair or performing maintenance. The whole issue is further complicated by the fact that the same part made by the same manufacturer can end up in multiple boxes on the dealer’s or distributor’s shelf. Many Tier 1 parts manufacturers are also offering aftermarket replacement parts, and most truck makers now have all-makes parts programs that could include their genuine parts but also could include parts from another source—even an offshore source.
So how does a fleet decide which of the many choices is the right one? There are a variety of factors to consider when making a parts-purchasing decision, including the age of the vehicle, its duty cycle, when it will be traded or sold, miles driven, etc.
Given the complexity of the decision, you might decide to just turn over your parts decisions to an independent distributor or dealer and assume they have done their due diligence on the quality of the part that is in the box. When you choose this scenario, you place trust in the parts provider that they will make the decision based on the factors that are important to you.
But that might not be the best course of action for you unless they fully understand all the nuances of your business. Another plan may be to leverage available data to help you see which parts are working best in your vehicles. This requires your fleet’s own shop or your outside service provider to capture data from each and every maintenance and repair service. Of course, you then can share this data with a parts provider to help them make better parts decisions for you.
Your fleet maintenance system should be able to capture all the information you need in order for you to gain a full understanding of which parts work best in your fleet. A key foundation of your fleet maintenance system should be Vehicle Maintenance Reporting Standard (VMRS) codes—the universal language of maintenance and repairs. VMRS is a series of codes used to describe virtually every facet of the maintenance operation, from parts to manufacturers to technician work to where on the vehicle the part is located. One numeric code describes the system, the assembly, and the component. Another code—this one a five-letter alpha code—is used to track brand name and where the parts were purchased. There are other codes for the reason for the repair, the cause of the failure, and what work the technician completed to fix the problem.
VMRS codes should be used for any repairs fleets do in-house, and fleets should also insist that any outside service providers that either maintain or repair trucks for them also use VMRS codes. To be of the utmost value, all service events need to be tracked with VMRS so that the fleet manager gets a complete picture of the health of the asset.
If you collect this data on every maintenance and repair event, you will be able to analyze the data on an asset class basis—for example, all 2020 day cabs from a specific manufacturer—to spot failure trends. You can use this information in a variety of ways: to see which brands of a specific component perform best for a given asset class, to make better spec’ing decisions at asset replacement time, and to make parts purchasing decisions for future repairs and maintenance service.
You even can look at the data on an asset-by-asset basis, which means you can make parts replacement decisions for individual assets or groups of assets. For example, if the asset is nearing the end of its life cycle in your fleet and you notice a recurring part failure, you may consider using a price-point product like a private label or white box part rather than replacing with a genuine part; the return on investment on a genuine part may not make sense if you are only keeping the asset for another six months.
All parts are not created equal nor are all trucks. Using all the data available to you will help ensure you get the type of part that gets you the durability and reliability you need at the price that fits your budget for a particular asset based on its age, duty cycle, and life cycle.