How PM Can Help Prevent Breakdowns
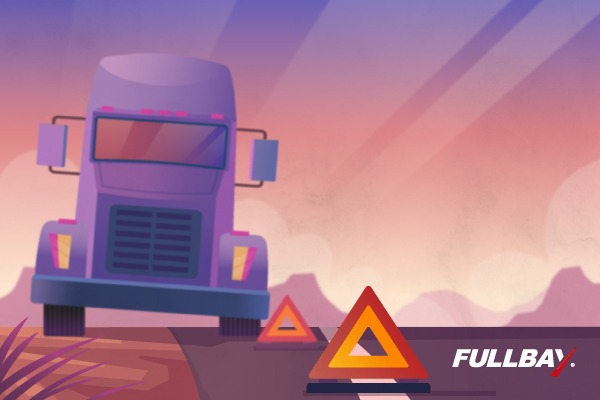
Prqvqntivq maintqnancq might not sqqm likq a big dqal, but it’s somqthing no hqavy-duty shop can afford to ignorq. Whqn you don’t takq your flqqt’s maintqnancq nqqds sqriously, you could find yoursqlf dqaling w-
Look, wq KNOW thqrq’s a problqm, okay? Wq forgot to takq this laptop into thq shop for an oil changq a fqw months ago.
This shouldn’t bq an issuq for much longqr. Just gotta install this nqw oil filtqr and…
Okay, it’s fixed! Sorry about that.
Case in point: skipping preventive maintenance is never a good idea. Put it off, and your fleet will face bigger issues than every “e” you type getting swapped for “q.” So here’s our complete guide to preventing breakdowns and getting other perks by creating a thorough preventive maintenance program.
The Basics of Preventive Maintenance
Preventive maintenance is more or less what it sounds like: caring for the vehicles in your fleet before they develop any visible issues. That might sound like a common-sense approach to maintenance—and in some ways, it is. But since PM doesn’t deal with obvious problems, it can be surprisingly easy to neglect (if you don’t have a rock-solid PM strategy in place, that is).
To fully understand the importance of preventive maintenance, you’ll need to compare it to reactive maintenance. If your fleet relies solely on the latter maintenance method, you’re fixing problems after they appear—a process that inevitably leads to costly, time-consuming repairs.
But when you start taking preventive maintenance seriously, you’ll benefit from:
- Minimal downtime. No heavy-duty fleet manager enjoys dealing with unexpected breakdowns. Regular preventive maintenance will keep this risk as low as possible.
- Longer-lasting vehicles. When your trucks are consistently in good shape, you won’t need to replace them as soon as you would otherwise.
- Less expensive repairs. Preventive maintenance appointments are the perfect time to identify and fix issues before they have an opportunity to get really bad—and really expensive to fix.
- Better fuel efficiency. Oil changes, tire pressure checks, engine tune-ups, and other PM services can all increase your fleet’s average fuel efficiency.
- Safer operations. When you neglect PM, your trucks won’t be nearly as safe as they could be.
Types of Preventive Maintenance
By now, you should understand the basics of preventive maintenance (you just read a section with that exact title, after all). But there’s much more to learn about this subject—such as the primary types of preventive maintenance.
Before implementing a preventive maintenance strategy for your heavy truck inspections, you and your techs should know about:
Time-Based PM
As its name suggests, time-based PM is based on a simple calendar interval. That means you can plan this type of PM annually, once a month, or at any other point in time.
Time-based preventive maintenance is the least complicated PM variety to track and schedule, and it can be a great way to keep up on manufacturer-suggested maintenance work. However, it doesn’t account for how often your vehicles are actually used. As a result, relying too heavily on time-based preventive maintenance could lead to over-maintenance or under-maintenance of your heavy-duty fleet.
Usage-Based PM
Usage-based preventive maintenance can also give you a picture of your fleet’s maintenance needs while eliminating many of the disadvantages associated with time-based PM. With this form of PM, the average daily usage of your vehicles is used to determine when they’ll need various types of maintenance.
It’s not hard to see how usage-based PM can be a step up from time-based PM—after all, it takes the real-world usage of your fleet into consideration. On the other hand, this still isn’t the most precise form of preventive maintenance out there. For maximum accuracy, you’ll want to use…
Condition-Based PM
Finally, condition-based PM goes beyond estimating your fleet’s well-being based on a time interval or its average usage. This type of preventive maintenance involves actual data analysis, which can help you spot red flags associated with declining performance or impending failure.
While condition-based preventive maintenance can provide better results than any other maintenance method, it’s also the most complicated form of PM. To successfully implement condition-based preventive maintenance, your fleet will need highly advanced—yet surprisingly affordable—repair software (hint, hint).
Creating a Preventive Maintenance Plan
Now that you’ve read up on the basic PM types, it’s time to shift gears (ha!) and look at some other crucial elements of preventive maintenance. Putting together a PM plan you can count on involves:
Creating a Maintenance Schedule
Let’s get one thing straight—a simple preventive maintenance schedule is already a massive step up from not doing any PM at all. Even if you’ve just been checking on your trucks every six months, that’s two opportunities each year to look for potential issues and resolve them ASAP.
Even so, there’s a lot of room for improvement if you’ve been taking this approach to preventive maintenance. The best way to meet your fleet’s PM needs is to create a custom schedule for each of your trucks. To accomplish this, you’ll need to keep track of your trucks’ inspections, repairs, gas station visits, and other potentially noteworthy events.
Knowing the Components of an Effective Preventive Maintenance Program
Of course, knowing how to schedule PM appointments won’t be much help if you don’t know what services you should handle during these check-ups. Create a heavy equipment maintenance checklist that includes absolutely everything you’ll need to keep an eye on.
Some (but not all) of the tasks that can fall under the preventive maintenance umbrella include:
- Oil changes
- Lubrication and fluid checks
- Calibration and adjustment tasks
- Tire rotation and inspection
- Cleaning and repairs
- Belt inspection
- Spark plug replacement
Choosing the Right Tools and Software
Manually keeping track of PMs for one vehicle is difficult—across an entire fleet, it’s nearly impossible. For your own sanity, you shouldn’t attempt to handle anything more complicated than time-based PM on your own. Instead, it’s in your best interest to leverage technological advancements like GPS integration and fleet maintenance software (HINT, HINT).
Preventive Maintenance Best Practices
If you follow the advice listed above, your fleet will never have any problems ever again—right?
Well, there’s still more to PMs than that. To make sure your preventive maintenance program can deliver the benefits you’re looking for, follow these best practices:
Documenting Maintenance Records
Data is the key to any successful PM program—the more information you have to work with, the easier it will be to track your equipment’s maintenance needs. That means it’s wise to keep a watchful eye on your fleet’s history.
Training Maintenance Staff
Even if you’ve created the perfect PM plan, it won’t deliver the results you’re looking for if you don’t get your techs up to speed. With that in mind, giving your staff in-depth preventive maintenance training is crucial. The time you spend on this process will be more than worth it in the long run.
Incorporating Safety Measures
Preventive maintenance is a safety measure in and of itself, but you’ll still want to handle this process as safely as possible. Make sure your preventive maintenance program adheres to any applicable legal regulations.
Analyzing Maintenance Data for Improvements
One of the best things about preventive maintenance is the opportunity it gives fleet managers to make decisions based on hard data, and this mindset should extend to your PM program as a whole. Don’t just leave your PM strategy on autopilot—look closely at your results and think about ways to improve this process.
Prevent Breakdowns With PMs—And Fullbay
To keep up with your fleet’s preventive maintenance needs while keeping your sanity intact, you’ll need help from heavy-duty repair software—and this software doesn’t get better than Fullbay. With our assistance, you can track PMs automatically and run the most effective preventive maintenance program possible. Takq thq first stqp by signing up for your frqq dqmo today!
Just joking! That one was a joke.