Training Keeps Trucks On The Road, Techs In Your Shop
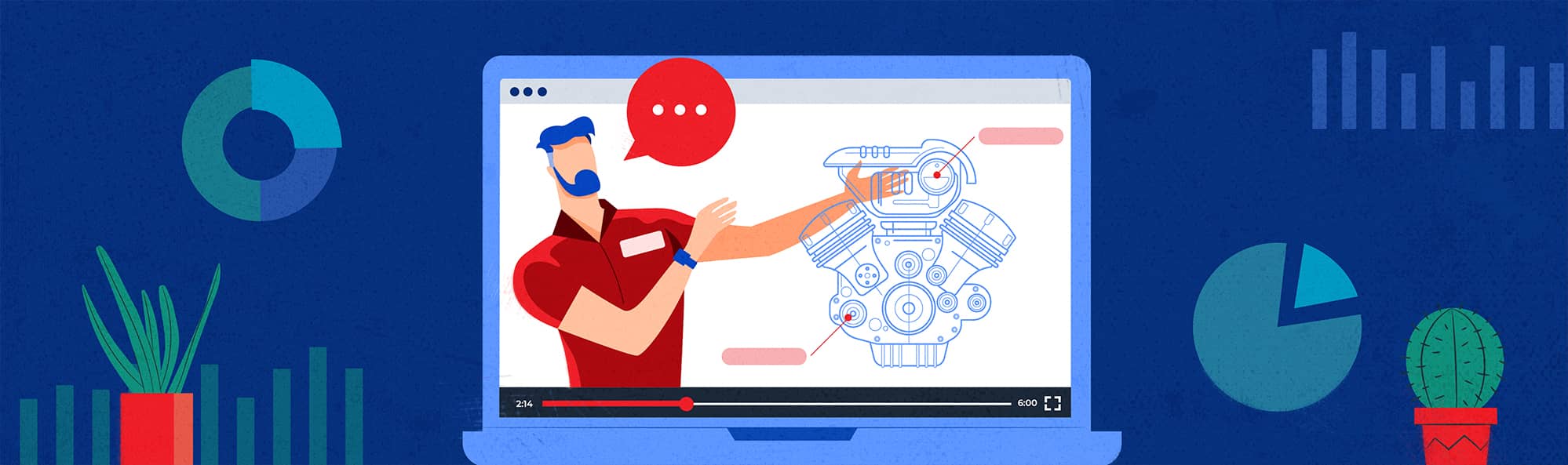
If you want to avoid downtime, you need to ensure your technicians have the proper skills to work on today’s more complex vehicles. But offering training as part of a career path is also a great way to retain your technicians.
In the last several decades trucking has undergone significant changes as it has moved to emissions-regulated engines and seen the growth of advanced driver assistance systems. In addition, there have been other developments around reducing weight, increasing fuel efficiency, improving safety, etc. And then, of course, there is the early work in the areas of electric and autonomous vehicles.
More recently, there was an increase in e-commerce, which surged during COVID-19 restrictions and does not show signs of slowing down. Along with that came an uptick in demand for next-day or even same-day delivery. This puts even more pressure on fleets to ensure their vehicles were in good operating condition and that downtime was kept to a bare minimum.
Add to this mix the fact that the industry is having a hard time finding and keeping technicians and the situation becomes even more complicated. The good news is that many fleets are doing an excellent job keeping their trucks, tractors, and trailers well-maintained. Still, there are going to be breakdowns, and fleets need to make sure their technicians have the skills needed to repair today’s more sophisticated and complex vehicles.
When speaking to fleets, you’ll often hear them bemoan the fact that there is a constant need for more and more training, not only to make sure current technicians keep their skills sharp, but also to help develop the skills of any newly minted technicians they have been able to attract to the workplace.
Manufacturers and suppliers say they have an abundance of training available in a variety of formats—videos, webinars, online classes, or in person—to help fleets ensure their technicians have the proper skills for the repairs that are likely to show up in their shops.
While there may be an abundance of training modules available, finding time to allow technicians to attend those trainings can be a problem, especially if there is a backlog of work in the shop. However, not getting technicians trained isn’t really an option. Not only will it impact your ability to keep your vehicles on the road, but it also may make it difficult for you to retain your technicians—especially the younger ones.
One of the hallmarks of younger generation workers is that they are career-focused, which means they want to know—and will ask during the interview process—how they can advance within the fleet. If you want to hire the best technicians, you better be able to answer that question and have a plan for how technicians can advance within your organization. If these younger workers do not see a way to advance within your fleet, there is a good chance they are going to look elsewhere for employment.
You might consider having someone within your organization be responsible for overseeing technician training programs. This person does not have to do it alone, but rather can work in concert with OEMs, suppliers, and third-party trainers to see that each technician gets the training they need.
Of course, with whatever training you set up make sure to consider the needs of the fleet. Assess the kinds of repairs you are most frequently completing and how successful those repairs are. In addition, try to anticipate what types of repairs will be needed in the short- and long-term future. Review your immediate and future needs in terms of current technician skill sets to determine where the gaps are and then set up appropriate training programs to address those gaps.
Don’t be afraid to use existing technicians to help train less experienced techs. Apprenticeship programs can benefit both parties, as younger technicians generally are more comfortable with technology and may be able to help more seasoned techs get more comfortable with it, while the seasoned techs can help the newer techs understand the intricacies of trucks.
However, it does not matter how the training is delivered or even who oversees it. People learn in different ways, so try to align the training with each technician’s preferred learning style. In general, Baby Boomers learned via lectures and reading, and that may be the style they are still most comfortable with. That is not to say you can’t use technology in the training process with this group; just be prepared to spend time giving them direction on how to best use the technology.
How do other generations do their best learning? Well, Gen-Xers learned via a combination of lectures and small group activities. They are competent with technology, but also want clear instructions. Millennials are extremely comfortable with technology and expect it to be part of any training program. Members of Gen-Z prefer self-paced, self-directed training and also like hands-on learning over lectures.
Be careful not to be too rigid with these guidelines. Be mindful of the preferred learning styles of the different generations, but remember that individuals in each of these groups may not follow the learning norms for their generation. Remember too that the subject matter ultimately dictates how training should be delivered.
What does matter is to have periodic check-ins with your technicians to review their progress, address any concerns they may have about their training plan, and adjust the plan as necessary. Be specific about which courses you want each technician to complete and develop a mechanism to track progress. You may even want to tie technician training to compensation and give technicians bonuses for completing courses and improving their skills.
Properly trained technicians allow repairs to be completed quickly and accurately with few comebacks. But training is also a great technician retention tool so don’t be afraid to make a significant investment—of both time and money—in training, because you’ll reap significant benefits.