Setting an Optimal Quantity Threshold
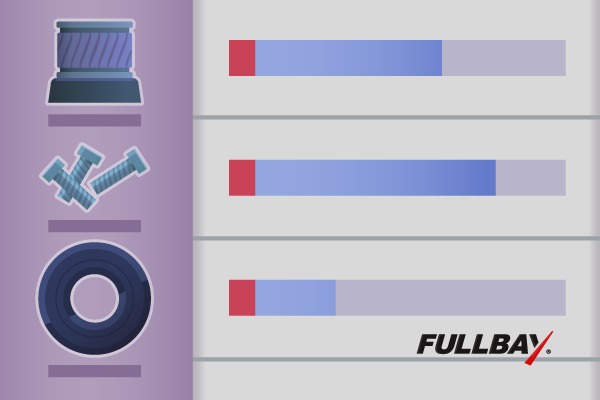
Taking control of your shop’s inventory extends beyond counting it on a regular basis. It also means managing parts on hand so that you have enough to do business without under or overstocking. Maintaining an ideal level of inventory is a balancing act. It involves many factors, and a few of them can be fluid rather than hard, unchanging numbers. Taking things like vendor minimums, sales history, and carrying costs into consideration helps you determine a healthy quantity threshold for each part in your inventory. Doing so will essentially automate your ordering process and ensure you don’t run out or buy more than you need.
What is a Quantity Threshold?
Before you can set a quantity threshold, it helps to understand what it is and how it works. The threshold on any given part is the minimum number you need to have in the stockroom at all times. It’s the number that ensures you have enough to complete jobs in progress with plenty to spare if an unexpected service or repair pops up. When the inventory level drops to the threshold, you know it’s time to place an order for more.
Figuring an ideal quantity threshold for every part you use is essential. If you don’t set a minimum amount, you could “stock out”—that’s when you run out of frequently used parts. That can cause delays and cost you jobs. In turn, it can also affect your reputation with customers.
Factors That Affect It
Many factors go into determining a quantity threshold. Part type is one, and you’ll have a different threshold for the different parts you carry. That’s because you use some more frequently than others. Vendor pricing also plays a role. Typically, vendors offer free shipping or give price breaks if you order specific amounts of their product. That can result in over-stocking unless you keep an eye on service orders and counter sales. Many times, those factors can get your order over the hump to meet vendor requirements for reduced pricing and free shipping.
Determining a Reasonable Threshold
So, you know your shop’s history of use for every part in your stockroom as well as vendor pricing variables. There are still a few other elements that factor into determining a reasonable quantity threshold. First, you have to consider carrying costs. That’s the money that the inventory costs you above the price you pay for it. Carrying costs include:
- the cost of the space in the stockroom
- insurance costs
- the cost of money—debt service if you buy it on credit or decreased cash flow if you use cash on hand
- property tax on inventory that hasn’t been sold
Accounting and inventory experts estimate that it will cost you 20 to 30 percent of what you pay for inventory to have it on your stockroom shelf. That’s why carrying just the right amount of inventory without overstocking is vital.
Then, there’s the time it takes for you to place the order, for the vendor to fill the order, and for the parts to arrive at your shop. All things considered, you might feel it’s reasonable to set a quantity threshold at 10 filters, for example. However, if you don’t place the order until your inventory dwindles down to 10 and it will take 2 weeks for an order to arrive, you’ll need to nudge that number up a little so the order can be placed and on its way by the time you start running low.
Mastering Quantity Thresholds
Keeping track of inventory in a spreadsheet like Excel is somewhat useful because it provides information necessary to determine the right quantity threshold for the parts you stock. Plus, you can see at a glance when parts hit their threshold. However, Fullbay has a better solution. It sees the big picture when it comes to inventory, knowing what’s been ordered, what’s in your stockroom, what parts are being sold at the counter, and which ones your techs are using. What’s more, Fullbay lets you set thresholds for orders according to vendor minimums—and you can even give specific people in your shop the ability to override those thresholds. In addition to all that, the software keeps a history on your inventory, so you can adjust the quantity threshold on any part whenever you need to. Give Fullbay a try and let it make you the master of your shop’s inventory.